Brass forging is a metalworking process in which brass is heated to a high temperature and then shaped into a desired form using compressive forces, typically applied with a hammer or a press. The goal of brass forging is to create parts with enhanced mechanical properties, such as increased strength, ductility, and durability, which are often required for high-performance applications in industries like plumbing, automotive, aerospace, and more.
Key Steps in the Brass Forging Process:
- Heating:
- The brass material is heated in a furnace or induction heater to a specific temperature, usually around 700-900°C (1292-1652°F), depending on the specific brass alloy.
- The heat softens the brass, making it more malleable and easier to shape without cracking.
- Forging (Shaping):
- Once the brass reaches the proper temperature, it is placed in a forging die or directly under a hammer or press.
- Compressive force is applied to the hot brass, either manually with a hammer or mechanically with a press, to shape the material into the desired part.
- During this process, the brass undergoes plastic deformation, where the material flows to fill the die, taking on the shape of the mold.
- Brass can be open-die forged (where the material is compressed between flat dies) or closed-die forged (where the material is placed between two dies with a cavity in the shape of the final part).
- Cooling:
- After the brass has been shaped, it is allowed to cool naturally or through a controlled process (sometimes in water or air).
- The cooling rate can affect the final properties of the brass, including its strength, hardness, and grain structure.
- Finishing:
- Once cooled, the forged brass part may undergo several finishing processes such as machining, polishing, or surface treatment (such as anodizing or plating) to meet the final specifications.
- This may involve removing excess material, improving surface quality, or adding special coatings for corrosion resistance or aesthetic purposes.
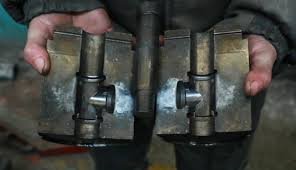
Advantages of Brass Forging:
- Enhanced Mechanical Properties:
- Strength: Brass forged parts typically have improved tensile strength and impact resistance compared to cast or machined parts, due to the refined grain structure created during forging.
- Ductility: Forging increases the material’s ductility, making it less prone to cracking and more flexible in applications that require bending or twisting.
- Durability:
- Forged brass parts tend to have higher fatigue resistance and are better able to withstand stress and wear over time.
- Design Flexibility:
- Brass forging can be used to create a wide variety of complex shapes, from simple parts like fittings and connectors to more intricate components like gears and valves.
- It allows for the creation of parts that are stronger and lighter than those made from cast brass.
- Cost-Effectiveness:
- While the initial tooling and setup costs for brass forging can be higher than casting or machining, the process is highly efficient for producing large quantities of parts.
- The need for less material wastage and the reduction in post-forging machining can lead to cost savings in the long run.
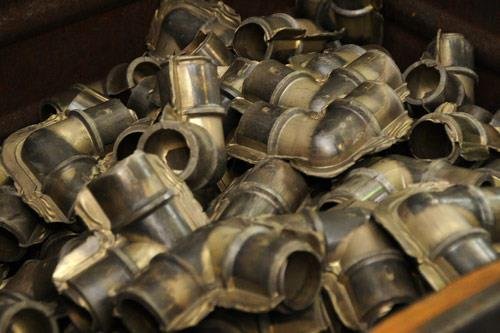
Types of Brass Alloys Used in Forging:
- CW617N (Free-Cutting Brass):
- This is one of the most commonly forged brass alloys, known for its excellent machinability. It contains around 57-59% copper and 35% zinc, with small amounts of lead to aid in machining.
- Used in applications where intricate parts with good machinability are required, such as valves, fittings, and plumbing components.
- CW602N (DZR Brass):
- A popular brass alloy used for forging, containing about 60% copper, 37% zinc, and small amounts of lead.
- This alloy is often used for creating durable components like valve bodies, fittings, and gears.
- C46500 (Naval Brass):
- This alloy includes copper, zinc, and 1-2% tin, providing excellent corrosion resistance in harsh environments like seawater.
- Used for marine hardware and other parts exposed to corrosive conditions.
- CW511L (Lead-Free Brass):
- This is a lead-free alloy that meets modern environmental regulations and is used for applications requiring strong corrosion resistance and high strength without lead content.
- Used in potable water systems, including fittings and plumbing components.
Applications of Brass Forging:
- Plumbing and Heating:
- Forged brass fittings, valves, and connectors are widely used in the plumbing industry, where durability and corrosion resistance are essential.
- Components such as thermostatic radiator valves, pressure relief valves, and shut-off valves are often made through forging.
- Automotive:
- Forged brass components like engine parts, brake fittings, and valves are used in the automotive industry due to their strength and resistance to wear and corrosion.
- Aerospace:
- Brass is sometimes used in aerospace components such as connectors, fasteners, and valves, where high strength and resistance to stress are required.
- Marine:
- Naval brass (C46500) is commonly used for marine hardware, including propellers, marine fittings, and seawater-resistant components, due to its excellent resistance to corrosion in saltwater environments.
- Electronics:
- Brass forging is also employed in the manufacturing of electrical connectors, switches, and other components requiring good conductivity and durability.
Conclusion:
Brass forging is a highly efficient process for creating strong, durable, and precision-engineered parts used in a wide range of industries, including plumbing, automotive, aerospace, and marine. The process enhances the mechanical properties of brass by refining its grain structure, resulting in improved strength, ductility, and corrosion resistance. Brass forged parts are essential in applications that demand reliability and longevity, especially in environments where high-performance materials are critical.
Choose IVALVECRAFT, choose reliable partner, enjoy the high quality and best service.