CNC (Computer Numerical Control) machining plays a crucial role in the processing of brass forging pieces, particularly when it comes to achieving precise dimensions, complex geometries, and smooth finishes that might be challenging to achieve through forging alone. Once the brass forging workpieces are shaped using the forging process, CNC machining is often employed to further refine the components, ensuring they meet the required specifications. This involves using computer-controlled machines like CNC lathes, mills, and drills to perform various operations.
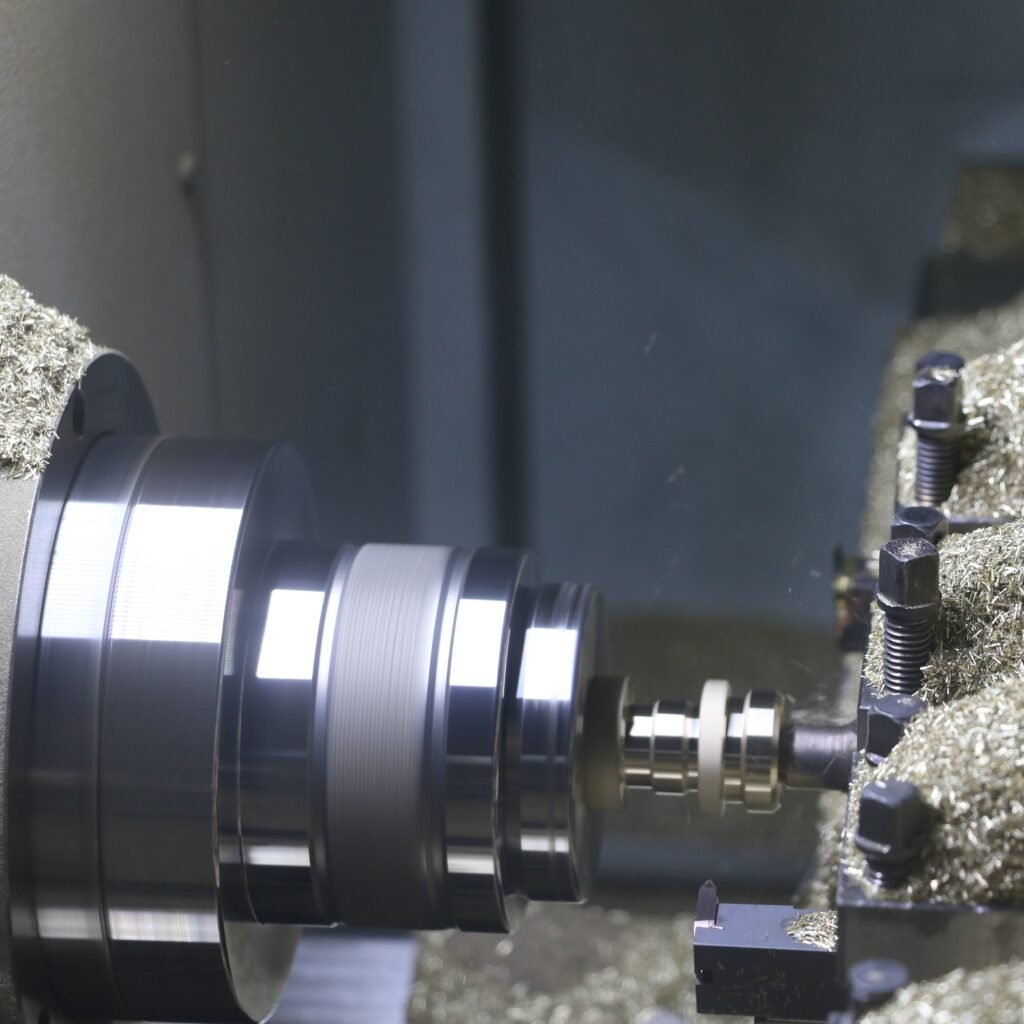
Steps Involved in CNC Processing Brass Forging Pieces:
1. Preparation of the Brass Forging Piece
- Inspection of Forged Pieces: After the forging process, the brass workpieces are carefully inspected for any visible defects, such as cracks, warping, or surface imperfections. Any excess material or flash that was formed during the forging process should be removed, typically via trimming or manual finishing.
- Fixture Setup: The brass forging piece is securely placed in a fixture or chuck on the CNC machine. The fixture holds the piece firmly in place to ensure stability during the machining process.
2. CNC Program Creation
- CAD Model: A 3D CAD (Computer-Aided Design) model of the forged piece is often created or imported. The CAD model provides the machine with exact dimensions, geometries, and features to be machined.
- CAM Software: Once the CAD model is created, it is fed into CAM (Computer-Aided Manufacturing) software. CAM software generates a CNC program based on the desired machining operations, toolpaths, speeds, and feeds.
- The CNC program contains specific instructions for the machine, such as the type of operation (e.g., turning, milling, drilling), the tools to use, and the path the tools should follow.
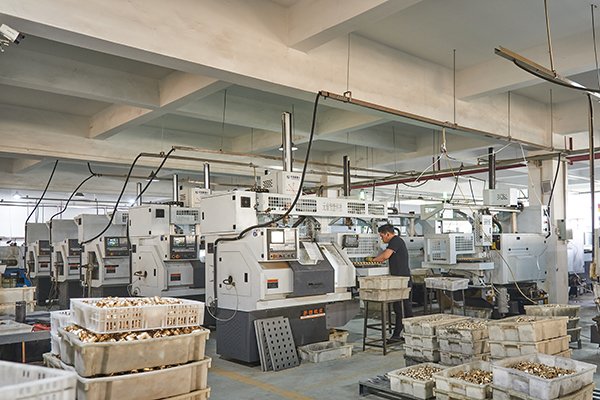
3. CNC Machining Operations
CNC machines can perform a variety of operations depending on the complexity of the forged part. The most common CNC operations used for processing brass forging pieces include:
a) Turning (Lathe Machining)
- Operation: For cylindrical or round brass forging pieces, CNC lathes are commonly used. The piece is rotated at high speed, while a cutting tool removes material to achieve the desired shape and finish.
- Features Machined: CNC turning is used to machine features like outer diameters, shoulders, tapers, and internal bores or threads.
- Process: The lathe cuts the brass piece along its rotation axis, providing high accuracy and smooth surface finishes. b) Milling (CNC Milling Machines)
- Operation: CNC milling machines use rotating cutting tools to remove material from the brass forging piece. The piece remains stationary or may be moved along multiple axes (typically 3 or 5 axes) for more complex shapes.
- Features Machined: Milling is ideal for cutting flat surfaces, creating slots, pockets, holes, geometries, and contours.
- Process: In 3-axis milling, the cutting tool moves along the X, Y, and Z axes. In 5-axis milling, the tool can move along additional axes to create complex features or surfaces. c) Drilling
- Operation: CNC drilling machines are used to create precise holes or bores in the brass forging piece.
- Features Machined: Holes for bolts, fasteners, or fluid passages are commonly created during this process.
- Process: The CNC drill is positioned over the workpiece, and a rotating drill bit is used to bore a hole to the required diameter and depth. d) Thread Cutting
- Operation: CNC machines can also be used to cut threads into the brass forging piece, whether external (on the outside of the piece) or internal (inside the piece).
- Features Machined: This is crucial for components like nuts, bolts, and fittings, where precise threading is essential for assembly or sealing. e) Surface Finishing and Polishing
- Operation: CNC machines can be equipped with tools for polishing or finishing the brass forging pieces to achieve smooth, shiny, or textured surfaces.
- Process: Polishing operations on CNC machines ensure a smooth surface finish that is free of imperfections and fits the requirements for aesthetic or functional purposes.
4. Coolant and Lubrication
- During CNC machining, coolants or lubricants are used to reduce the heat generated by the cutting process. Brass, being a relatively soft material, can produce significant heat when machined at high speeds.
- Coolants also help to extend the life of the cutting tools and improve the overall quality of the machined surface by reducing friction and preventing thermal damage to the brass.
5. Precision Measurement and Quality Control
- Dimensional Accuracy: After machining, the brass forging pieces are carefully inspected for dimensional accuracy. This is typically done using precision measuring instruments such as calipers, micrometers, and CMM (Coordinate Measuring Machines).
- Surface Finish: The surface finish is also inspected using surface roughness testers or visual inspections to ensure that the part meets the desired quality standards.
- Tolerances: CNC machining allows for tight tolerances, ensuring that the brass workpieces are produced with high precision, which is especially important for parts that will be used in mechanical or structural applications.
6. Post-Machining Operations
After the machining is complete, several additional operations might be required to further refine the brass forging pieces:
- Heat Treatment: Some brass components may undergo heat treatment, such as annealing, to relieve stress and improve material properties like ductility and strength.
- Polishing and Deburring: Brass forging pieces can be polished or deburr to remove any sharp edges or burrs left from the machining process. This ensures smooth, safe edges and improved appearance.
- Plating or Coating: In some cases, brass parts may undergo plating or coating with materials such as nickel, chrome, or lacquer to improve corrosion resistance or enhance appearance.
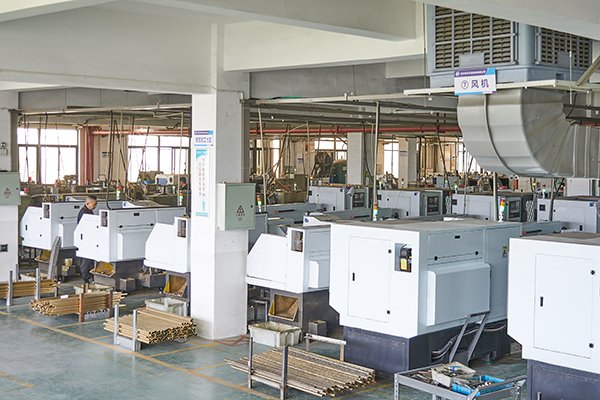
Advantages of CNC Processing for Brass Forging Pieces:
- Precision and Accuracy: CNC machines provide high levels of accuracy and can maintain tight tolerances, which is critical for parts that need to fit with other components or perform under specific conditions.
- Complex Geometries: CNC machining allows for the creation of complex shapes, such as intricate holes, pockets, or contours, that would be difficult or impossible to achieve using only the forging process.
- Repeatability: Once the CNC program is set, it can be used to produce identical parts with consistent quality, making it ideal for mass production or high-volume orders.
- Material Efficiency: CNC machining removes material only where needed, reducing waste and ensuring that each brass piece is used effectively.
- Reduced Labor Costs: CNC machines are automated, which reduces the need for manual labor and minimizes the risk of human error, improving both efficiency and overall part quality.
Conclusion:
CNC processing of brass forging pieces is a highly effective method for achieving precision, complex geometries, and high-quality finishes. The CNC process allows manufacturers to fine-tune the dimensions, add features like threads or holes, and improve the surface finish of forged brass components. By combining the strengths of both forging (for bulk shaping and enhanced mechanical properties) and CNC machining (for fine-tuning and precise feature creation), brass workpieces can meet the high standards required for a variety of industries, from plumbing and automotive to aerospace and electronics.
Choose IVALVECRAFT, choose reliable partner, enjoy the high quality and best service.