Struggling to maintain consistent pressure in your hydraulic system? Incorrectly adjusted hydraulic pressure relief valves can lead to equipment failure, costly downtime, and even safety hazards. The good news? Properly adjusting these valves ensures stable performance and protects your machinery. Dive into this guide to learn the step-by-step process and keep your operations running smoothly.
To adjust a hydraulic relief valve, locate the valve, loosen the locknut, and turn the adjustment screw clockwise to increase pressure or counterclockwise to decrease it. Use a pressure gauge to monitor changes, then tighten the locknut once the desired pressure is set.
This simple process is just the start. Read on to understand the role of hydraulic relief valves, their functions, and why precise adjustments matter for your system’s efficiency.
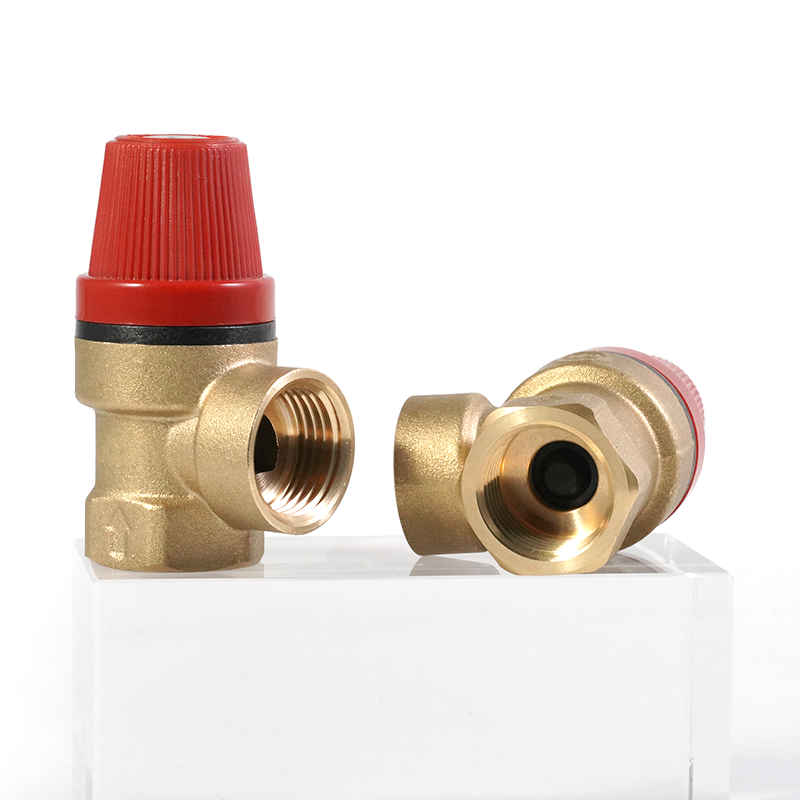
What Is the Basic Function of the Hydraulic System?
A hydraulic system powers machinery by using pressurized fluid to transmit energy. It’s like the heart of heavy equipment, pumping life into operations like construction, manufacturing, and plumbing. The system relies on components like pumps, actuators, and valves to control fluid flow and pressure. For example, in plumbing applications, hydraulic systems ensure consistent water pressure for heating or cooling systems.
The main relief valve in a hydraulic system plays a critical role by regulating pressure to prevent overloading. Without proper pressure control, components can wear out fast or even break. The hydraulic pressure relief valve working principle is simple: it opens to release excess pressure, protecting the system. Understanding this function helps you see why precise valve adjustments are vital for efficiency and safety, especially in high-stakes environments like large-scale construction or industrial plumbing.
What Are the Main Functions of Valves?
Valves are the gatekeepers of hydraulic systems, controlling the flow, pressure, and direction of fluid. They ensure your equipment runs smoothly without overloading or underperforming. The function of a pressure reducing valve in a hydraulic system is to maintain a steady downstream pressure, regardless of upstream fluctuations. This is crucial for applications like radiant heating systems, where consistent pressure ensures comfort and efficiency.
Then there’s the hydraulic pressure relief valve, which acts like a safety net. Its job is to release excess pressure to prevent damage. The hydraulic pressure relief valve types include direct-acting and pilot-operated valves, each suited for different pressure ranges and applications. For instance, in plumbing, a brass safety valve might be used to protect water heaters. Valves also direct fluid flow, ensuring it reaches the right components at the right time. Without valves, hydraulic systems would be chaotic, leading to inefficiencies or breakdowns.
What Is the Function of a Hydraulic Check Valve?
A hydraulic check valve ensures fluid flows in one direction only, preventing backflow that could disrupt or damage the system. Think of it as a one-way street for fluid. In plumbing, check valves are essential in systems like manifolds or mixing pump heating centers, where backflow could mess up pressure or temperature control. The hydraulic pressure relief valve symbol often appears in system diagrams alongside check valves, showing their complementary roles.
The check valve’s design is simple but effective, typically using a spring or gravity to close when flow reverses. This prevents contamination, maintains pressure stability, and protects pumps and other components. In a pressure relief valve circuit diagram, you’ll see how check valves work with relief valves to maintain system balance. For industries like construction or wholesale plumbing, reliable check valves mean fewer maintenance headaches and longer-lasting systems.
Why Is Adjusting a Hydraulic Relief Valve Important?
Adjusting a hydraulic relief valve isn’t just a maintenance task; it’s a game-changer for system performance. The hydraulic pressure relief valve adjustment process ensures the valve opens at the right pressure, preventing over-pressurization. Too high, and you risk damaging components; too low, and the system may not deliver enough power. For example, in a thermostatic mixing valve setup, precise pressure settings ensure consistent water temperature.
The hydraulic pressure relief valve diagram shows how the valve interacts with other components. By adjusting it, you’re fine-tuning the entire system’s efficiency. This is especially critical for B2B clients like building materials wholesalers or construction procurement teams, who rely on dependable systems to meet tight project deadlines. Regular adjustments also extend equipment lifespan, saving costs on replacements and repairs.
Common Mistakes When Adjusting Hydraulic Relief Valves
Even pros can slip up when adjusting hydraulic relief valves. One common mistake is ignoring the hydraulic pressure relief valve working principle and adjusting without a pressure gauge. This can lead to inaccurate settings, causing system inefficiencies or damage. Another error is not securing the locknut after adjustment, which can cause the valve to drift out of alignment over time.
Some overlook the importance of checking the hydraulic pressure relief valve types before adjusting. Direct-acting valves respond differently than pilot-operated ones, and using the wrong technique can throw off performance. Also, failing to inspect the valve for wear or debris can lead to inconsistent pressure control. For plumbing wholesalers or DIY chain stores, these mistakes can result in customer complaints or returned products, hurting your reputation.
Step-by-Step Guide to Adjusting a Hydraulic Relief Valve
Let’s break down the hydraulic pressure relief valve adjustment process clearly. First, identify the relief valve in your system—check the hydraulic pressure relief valve diagram if needed. Next, ensure the system is powered off for safety. Locate the adjustment screw and loosen the locknut. Using a screwdriver, turn the screw clockwise to increase pressure or counterclockwise to decrease it. Small turns are key—don’t overdo it.
Attach a pressure gauge to monitor real-time changes. Start the system and observe the gauge as you adjust. Once the desired pressure is reached, tighten the locknut to secure the setting. Double-check the pressure to confirm it’s stable. This process ensures your system, whether it’s for manifolds or pressure reducing valves, operates at peak performance, meeting the needs of clients like construction project managers.
How IVALVECRAFT Ensures Reliable Valve Performance
At IVALVECRAFT, we know that high-quality valves are the backbone of efficient hydraulic systems. Our brass safety valves, thermostatic radiator valves, and pressure reducing valves are designed for stable export pressure and sufficient flow rate. Whether you’re a purchasing officer for a large company or a plumbing wholesaler, our products meet the demands of tough applications in Russia, Poland, the UK, and beyond.
We use rigorous testing to ensure every valve performs reliably, reducing the need for frequent adjustments. Our hydraulic pressure relief valve types are built to handle diverse systems, from heating manifolds to industrial setups. By choosing IVALVECRAFT, you’re partnering with a manufacturer that prioritizes durability and customer satisfaction, helping you avoid costly downtime and maintenance issues.
Summary
Adjusting a hydraulic relief valve is critical for maintaining system efficiency and safety. By understanding the hydraulic pressure relief valve working principle, recognizing the roles of valves like check and pressure reducing valves, and following a precise adjustment process, you can optimize performance. Avoid common mistakes, use the right tools, and rely on high-quality products to keep your operations smooth. IVALVECRAFT’s valves, from brass safety valves to thermostatic mixing valves, deliver the reliability your business needs.
Choose IVALVECRAFT, choose a reliable partner, enjoy the high quality and best service.